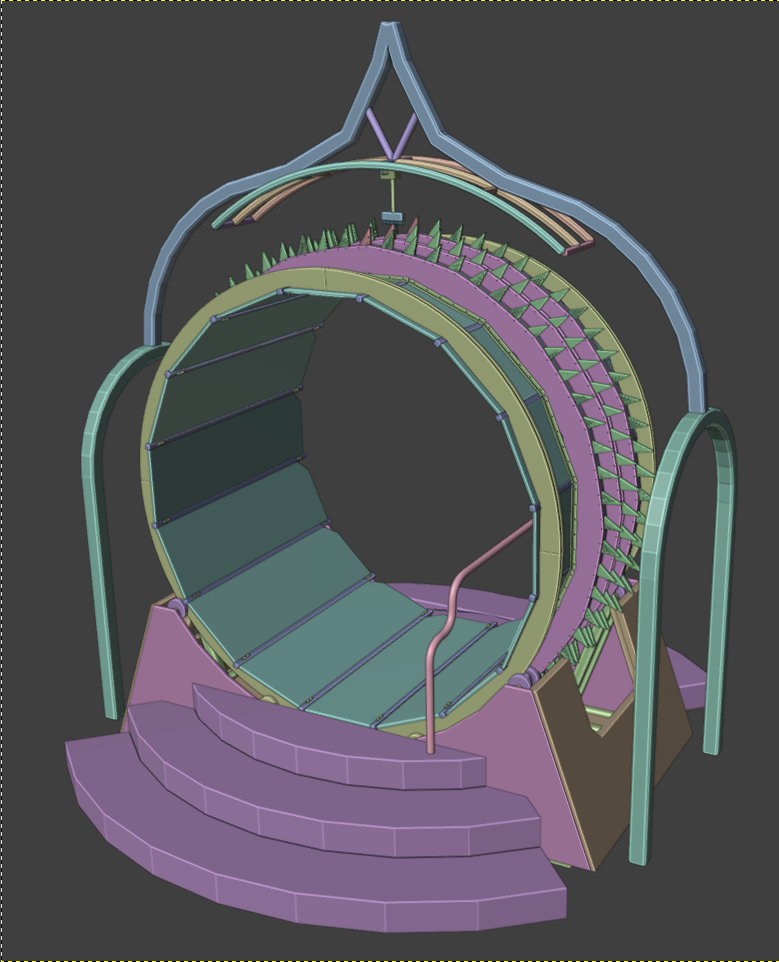
Loop is an analog human~powered rhythm generator manufacturing melodious moods. The power is generated by 1-3 persons walking inside the hamster wheel. Above the wheel there is a “trellis” (lattice) where kinetic sound-generating mechanisms will be attached. These will be triggered mechanically by arrangements of cams around the outside of the wheel. Cams can be rearranged to program the tunes. These cam interactions will also integrate LED light switches, accompanying each “beat” with a “blink.”
Project must be constructed in a modular way which makes assembly/disassembly and packing/shipping as efficient as possible.
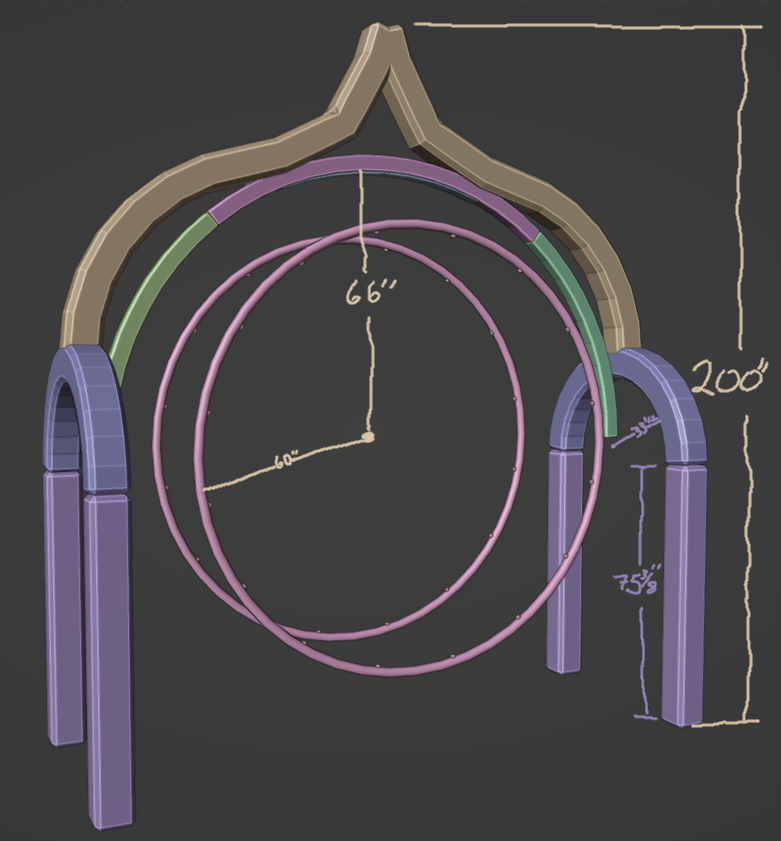
Total height of structure is ~17′, width side to side is ~14′, and depth around 15′ (including circular stairs). Hamster wheel diameter is 10′ (5′ radius) and depth is 6′. 3 circular steps (8″ tall per stair) lead up into and out of the wheel.
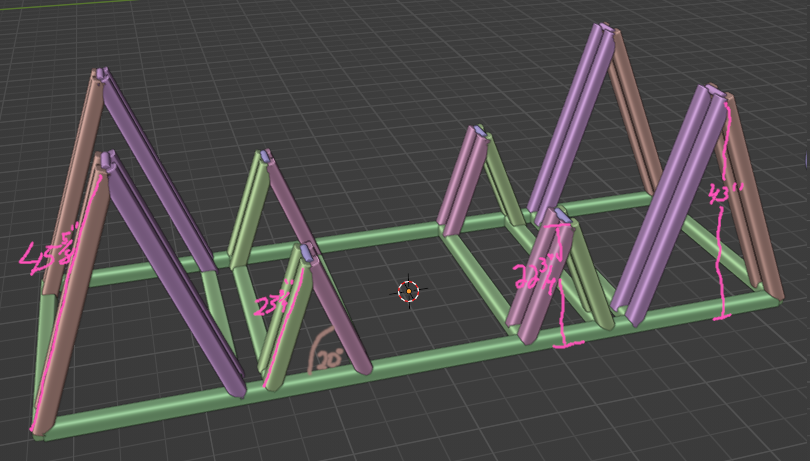
The wheel is supported by a base made of triangles with rollers at the apex of each triangle. The wheel is constructed of two outer steel rings (2″ square tubing?), with 1″ square tubing struts connecting them. 16 plywood planks between the struts form the walking surface inside the wheel.
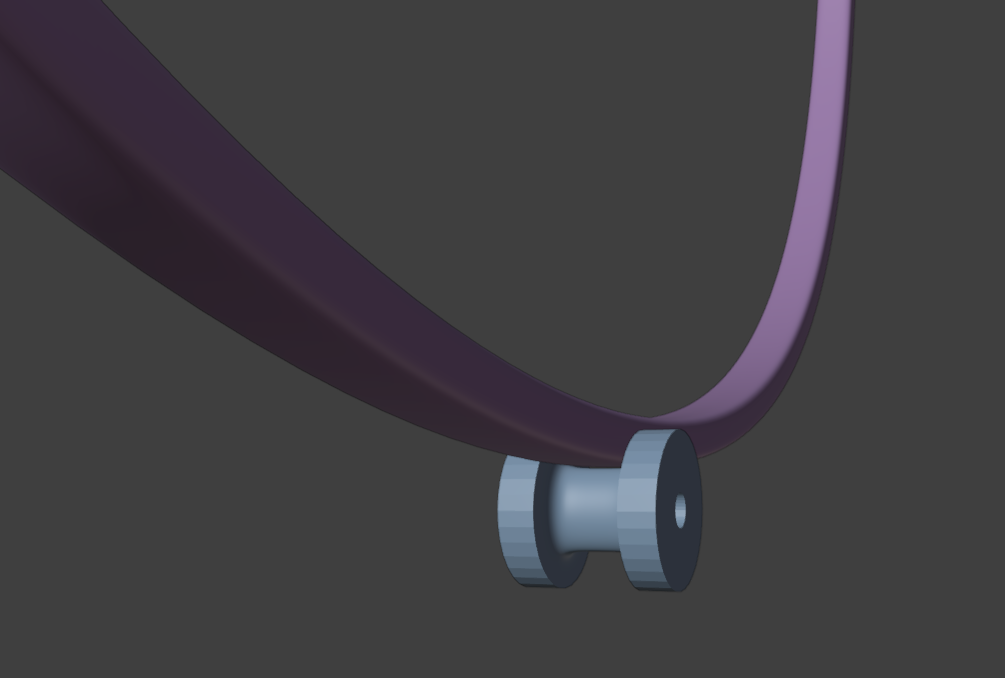
The outer steel rings function as “tracks” – they interface with the rollers, keeping the wheel from drifting sideways as it rolls.
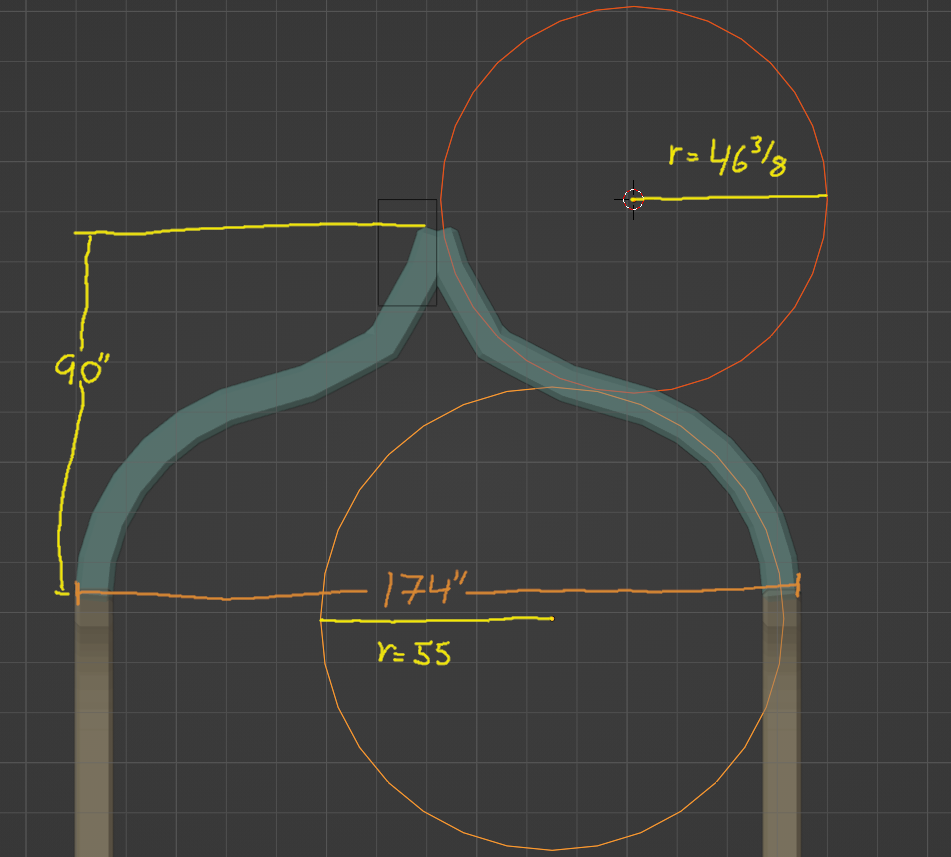
Production begins this fall – by fabricating the superstructure from the top down; cutting the profiles out of metal sheet using cnc plasma cutter in easily transportable pieces, and bolting them together into assemblies in a large barn.
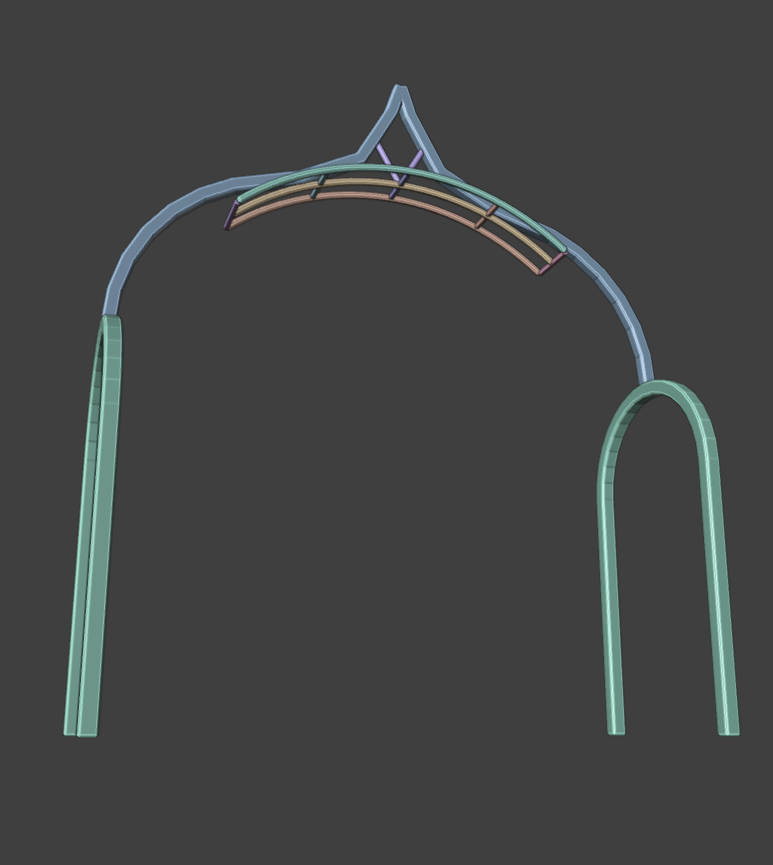
Next, the trellis will be constructed of a square tube bent into a semicircle of 66″ radius, then cut into 3 equal lengths and connected with 5 straight 3′ lengths of tubing.
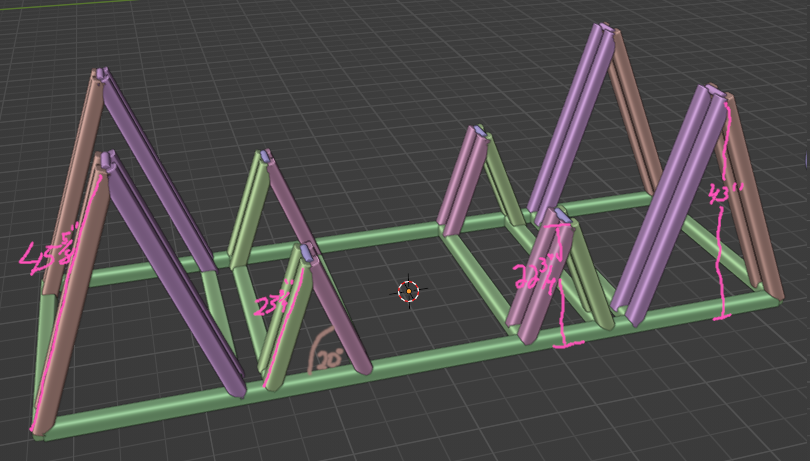
Next is the wheel base – first the flat triangles will be welded and assembled together with all parts but the long green tubes at the bottom; Leaving some room for adjustment. After the wheel tracks are ready, rollers will be added, base triangles will be positioned using the wheel tracks for final placement, and finally the long green tubes at the bottom will be connected to hold the base together.
Updated wheel/base/roller interface, with beefed up trusses to support the wheel, and a square tube ring on the rollers to act as a track with track guides.
With the trellis in place, percussion and instrument mechanisms can be mounted to it for testing sounds and programming.
Example of programmable cams to play melody or chords, as in this case. The cams can be locked in on/off position using a vertical rod/pin, to program which notes are triggered.
Potential cam update enables more notes to be played, depending on speed of wheel. a speed limiter mechanism may be useful, to keep BPM from getting too high.
Mechanism idea for extending length of loop beyond a single revolution of the wheel. Each time the instrument drops, it is exposed to a new row of cams.
A simplified, lightweight cam sequencing system can be created using pipes. The pegs (cams) can be prearranged on the ground, then easily swapped on and off the wheel.
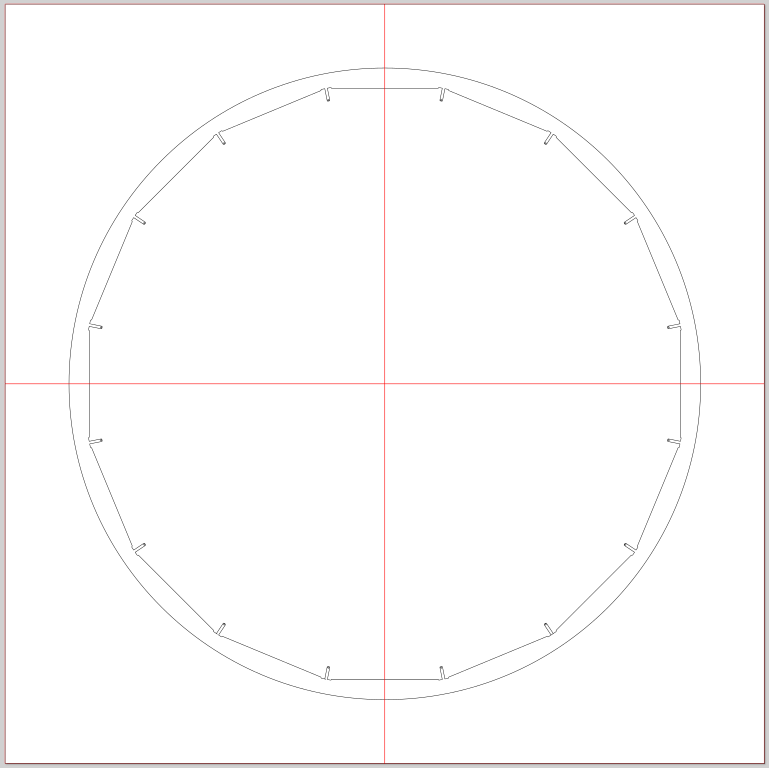
Wheel “tracks” profiles will be cut from flat sheet. This provides several advantages over bending square tubing: 1) avoids kinking, warping and other difficulties inherent in bending square tubing; 2) allows for breaking large rings down into 4 pieces and eliminates “springback” from bent metal circles; 3) allows for a custom inner profile including tabs and locking mechanism for precise and placement of struts and planks; 4) cnc plasma tool is readily available in workshop, whereas ring bender is not.
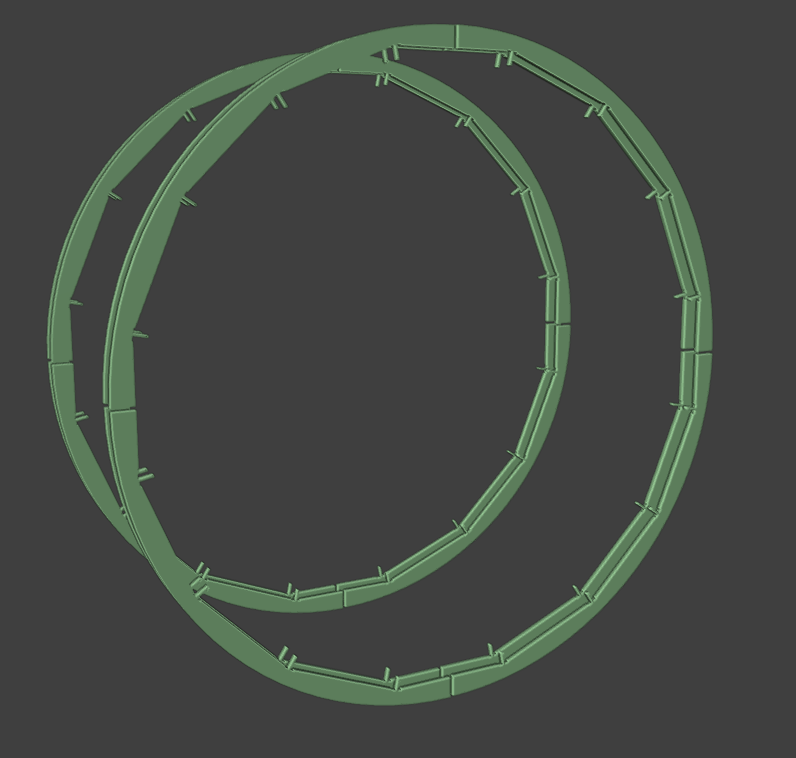
Hamster wheel “tracks” constructed in such a way serve as guides for wheel motion (outer circle,) and lock in the struts on the inside. These also make it possible to break up the big rings into quarters for modularity and ease of assembly and shipping.
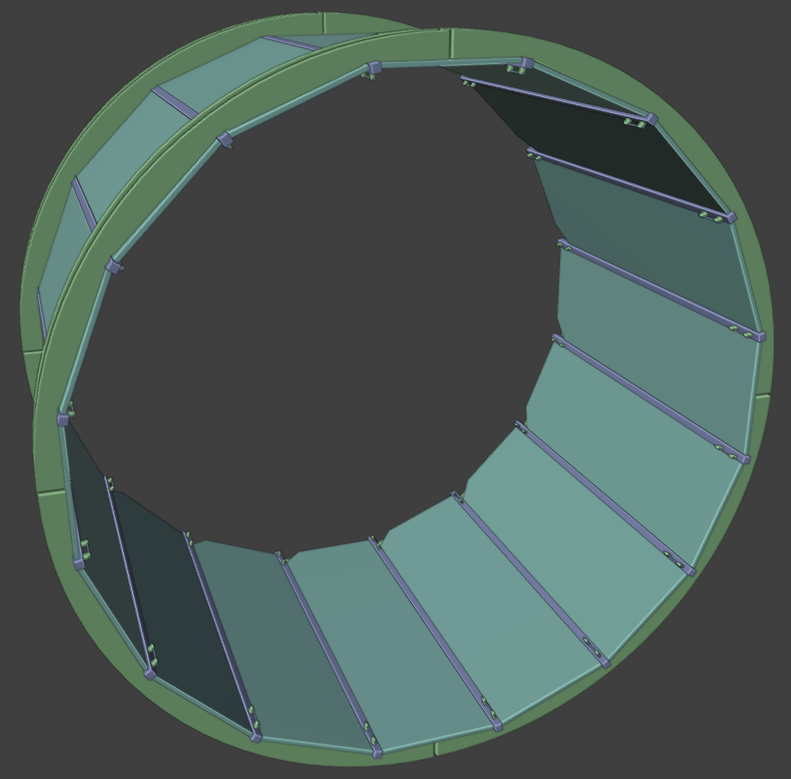
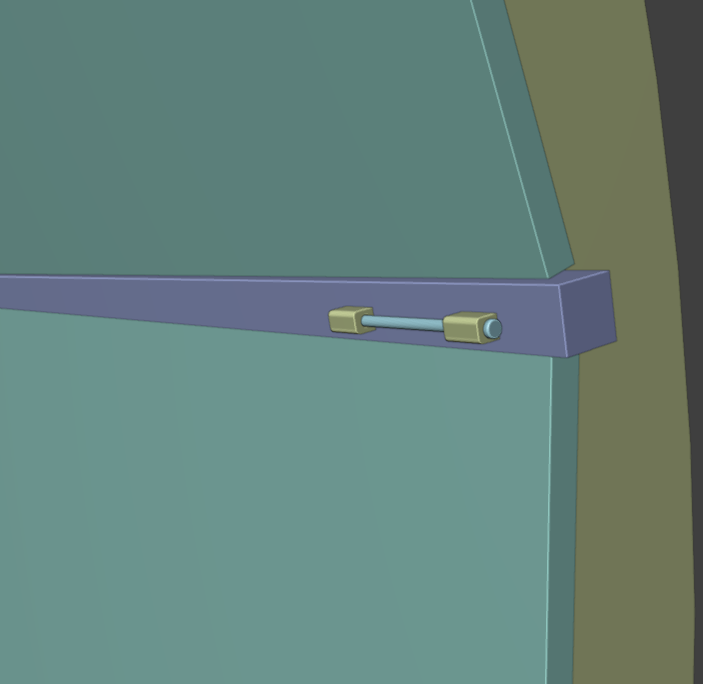
Closeup of strut locking mechanisms
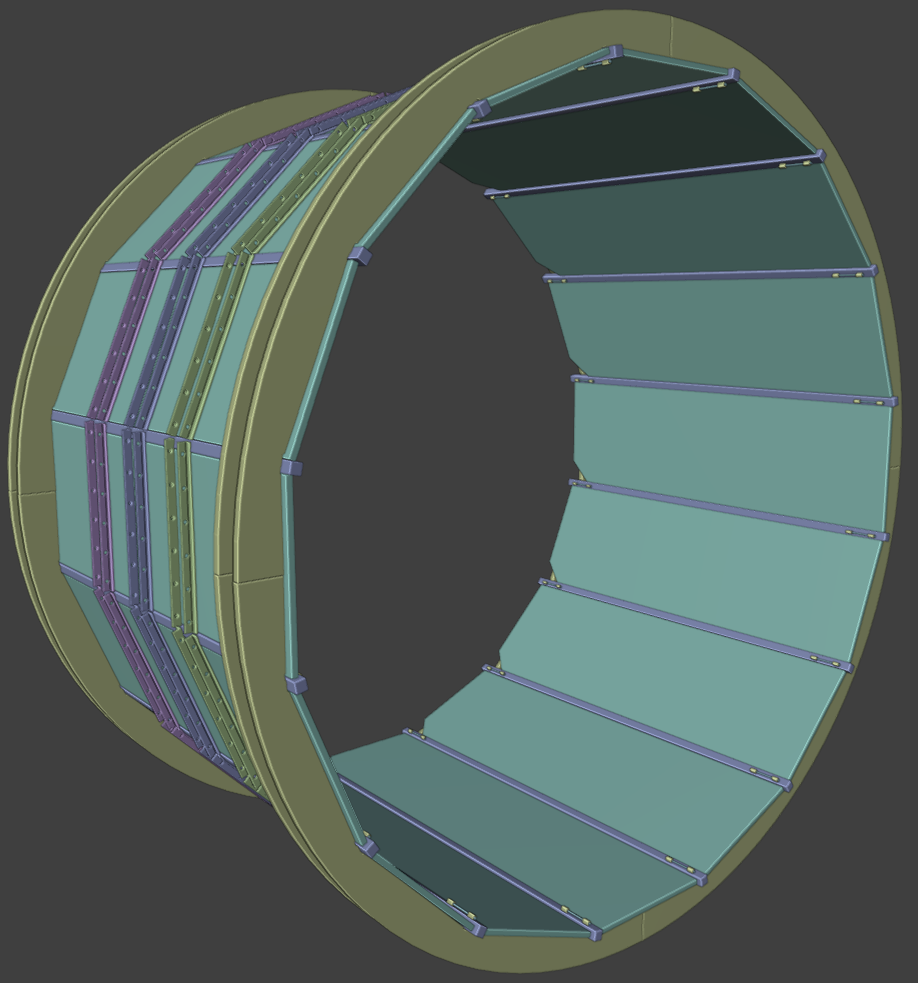
After wheel is constructed, angle irons will be added around the outer perimeter, attached to struts; these will have holes to function as rails for easily mounting and removing cams.
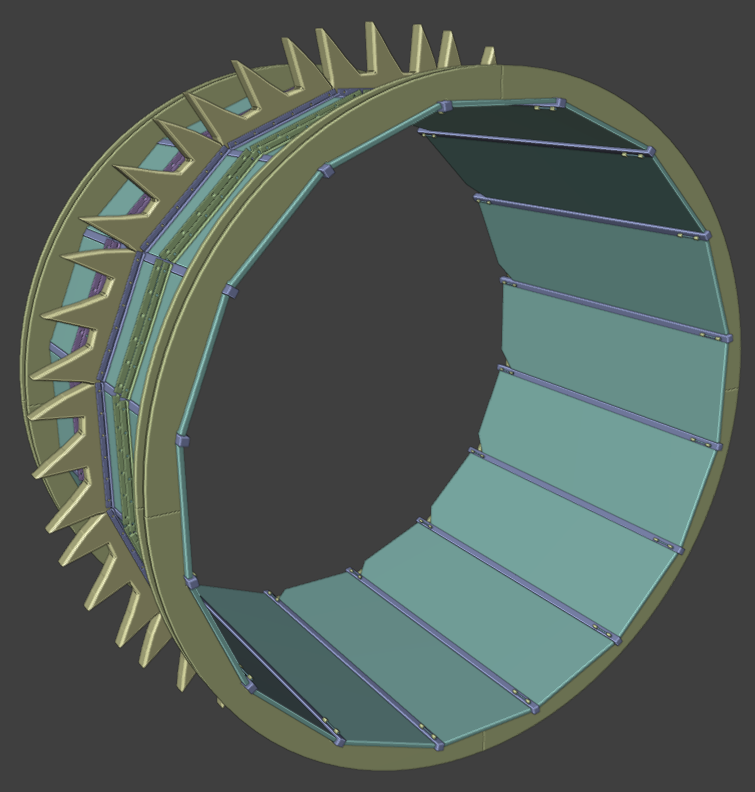
Example with cams mounted.
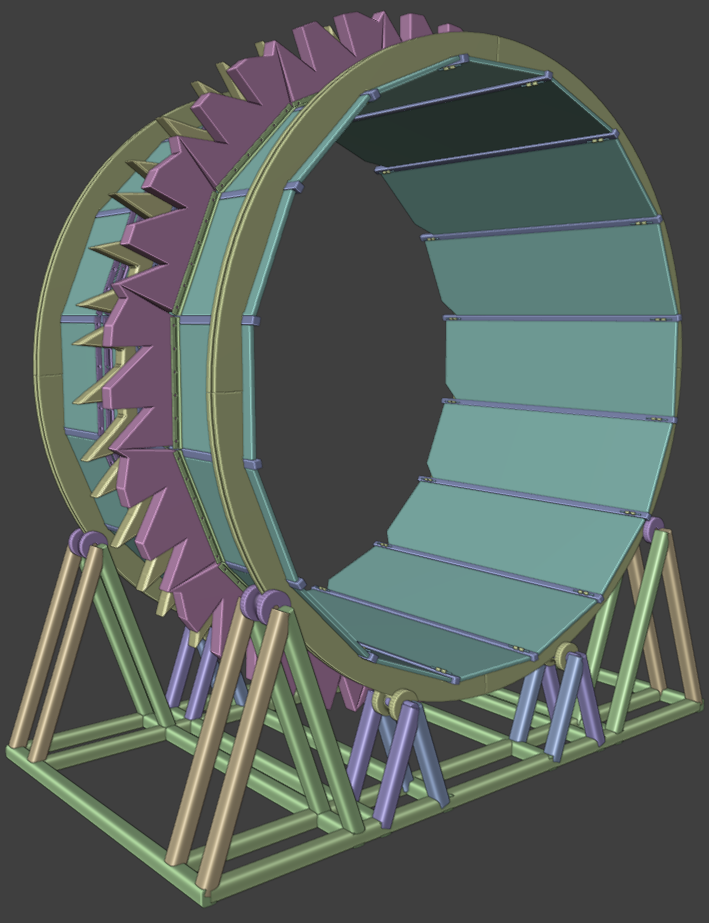
Wheel on base – base may need additional reinforcement (crossbars).
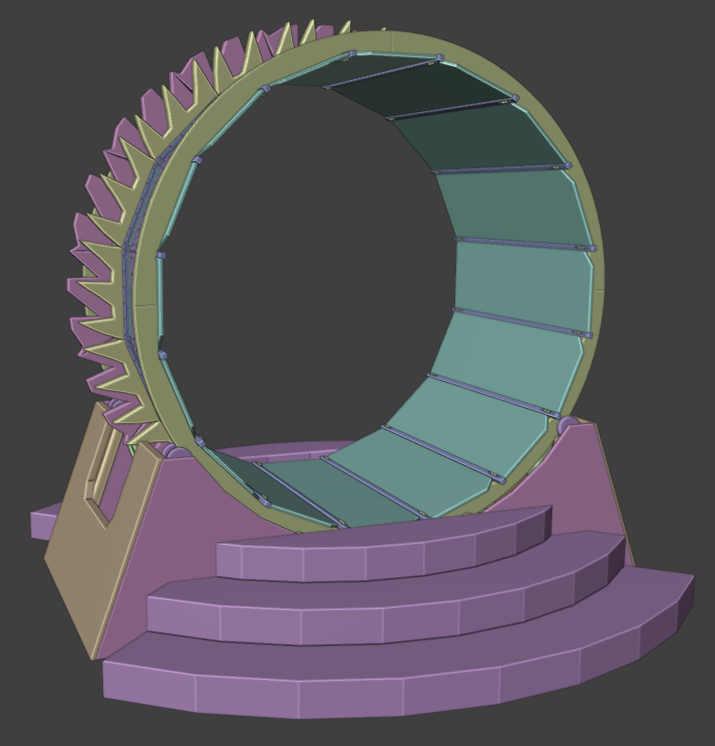
Now the circular steps are built, leading up and down from the wheel, and a plywood cover for the base is added.
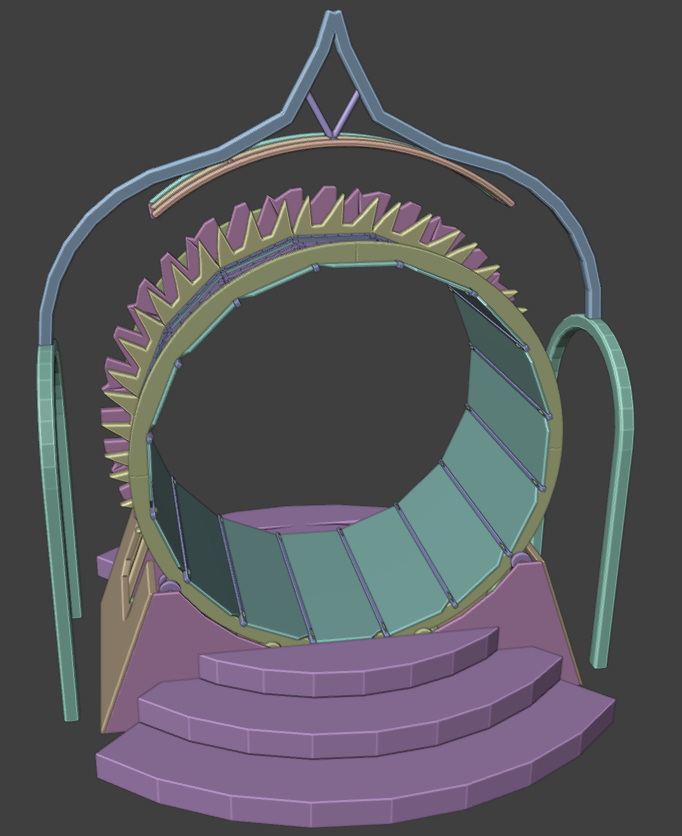
The structure and the wheel are put together.
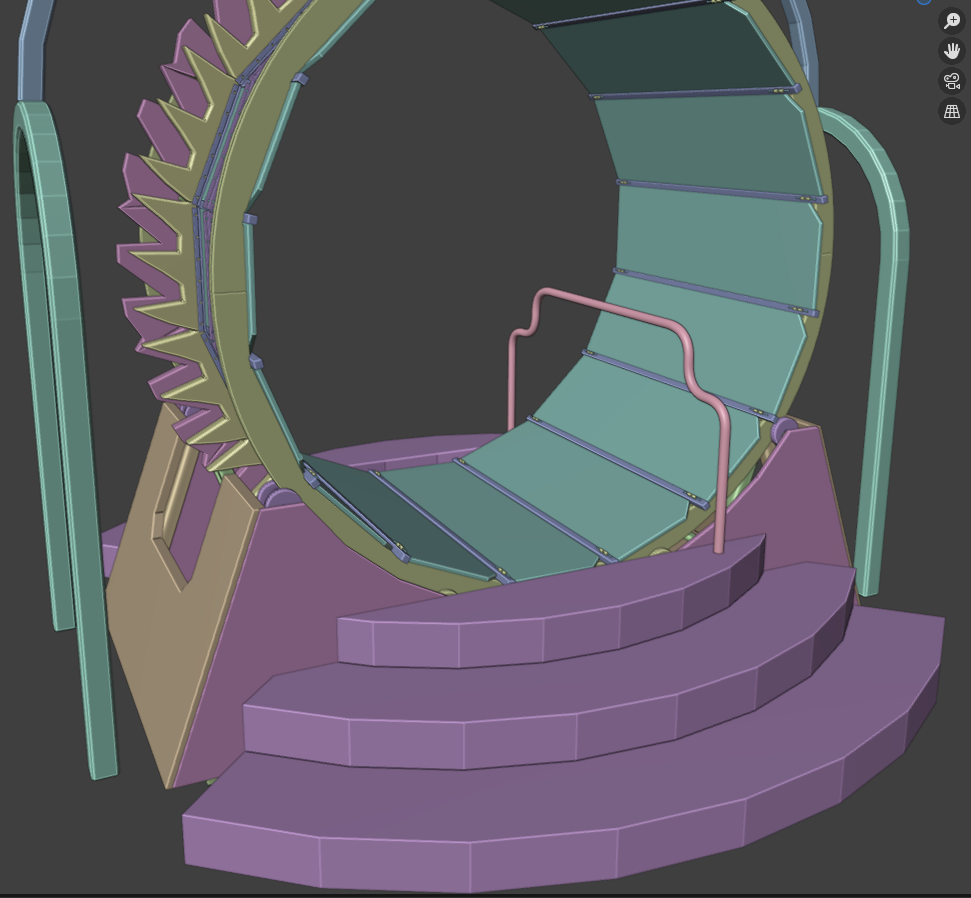
A handrail is added as safety precaution. Depending on the inertia, smoothness, and momentum generated by the weight and motion of the wheel, a brake may need to be added. The brake would function using friction. It would be released by gripping the handrail and engaged when rail is let go.
After experimenting with wheel motion, safety reinforcements and brake, it is time to add kinetic modules, starting with percussion. This is a part (upside-down) of a snare module which is compressed by aforementioned cams and then springs down to strike a drum. Inspired by the springy 15 second animation above.
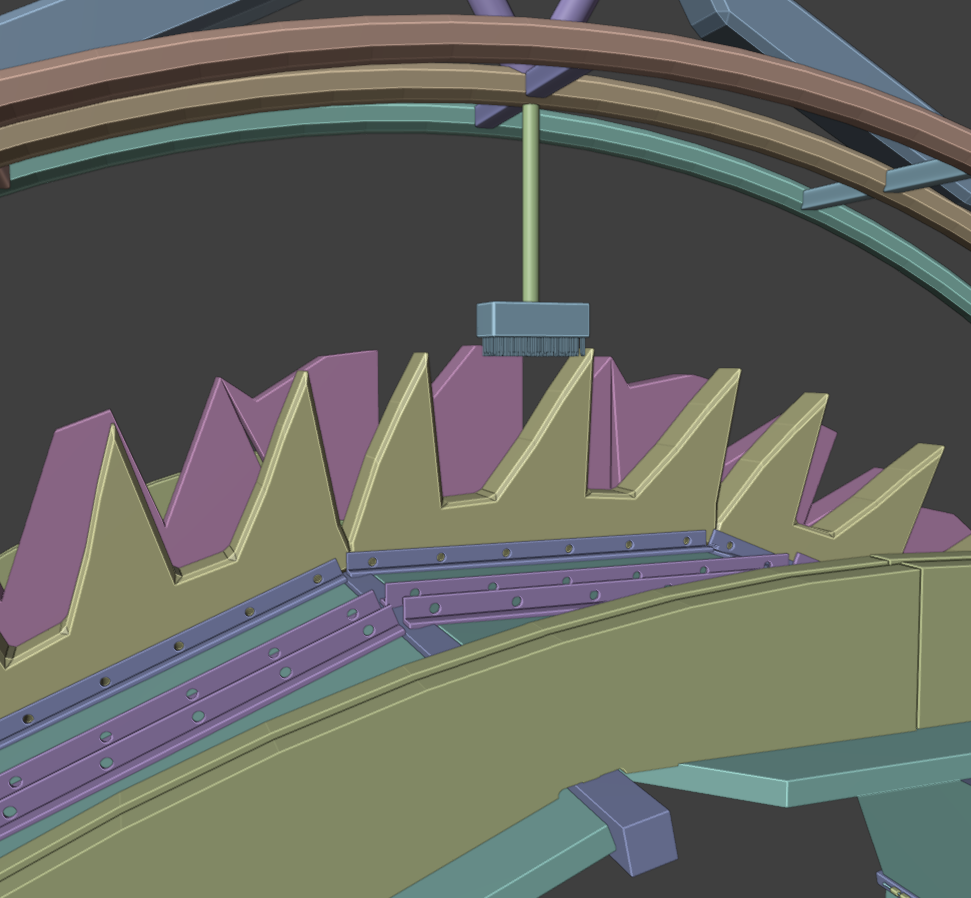
Here is a simpler percussive brush instrument where the cams scrub against a stiff-bristled brush to make an “open hi-hat” type sound. Using these two mechanisms or something similar, a kick/snare/hat rhythm can be programmed. Down the line, more cam tracks and modules can be added for melodic instruments.
This pivot and pin design makes it possible to fold and lock cams in either an “on” (play) or “off” (mute) position to reprogram the beats. Click animation to play.
To extend the capability of programming tunes longer than the number of cams allows, a simple “derailleur” type system can be used to move the instrument to play another track of cams. In this animation (click to play) we can see an example using a small wheel pushing against a triangular wedge, shifting the brush assembly to play a new rhythm. note: not gonna work!
A simple concept for percussion. Bolts acting as cams, can be used in different arrangements to change rhythms.
These interactions between cam and module must also trigger switches to turn LEDs on and off.
Plan for mockup construction
Mockup in progress
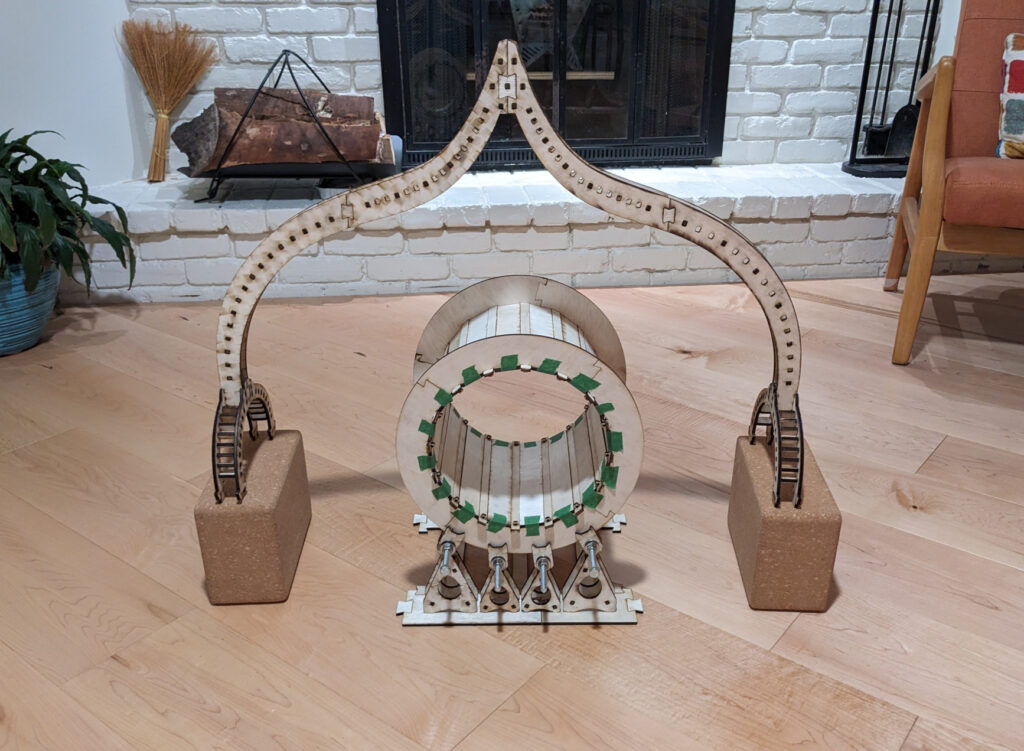
Outer structure (sans legs)
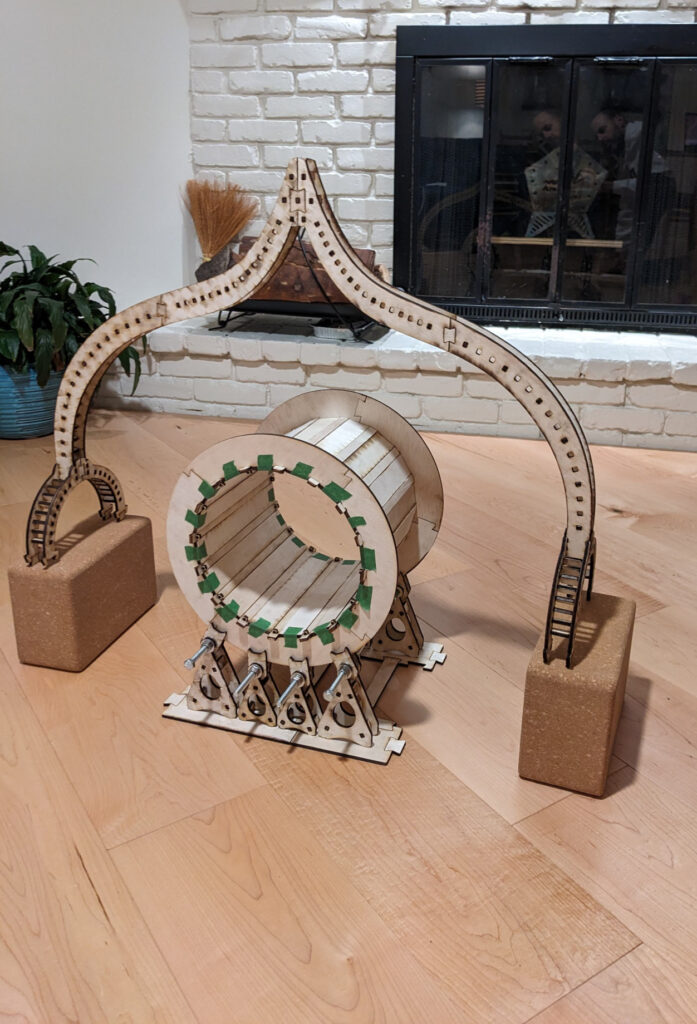
Outer structure in progress
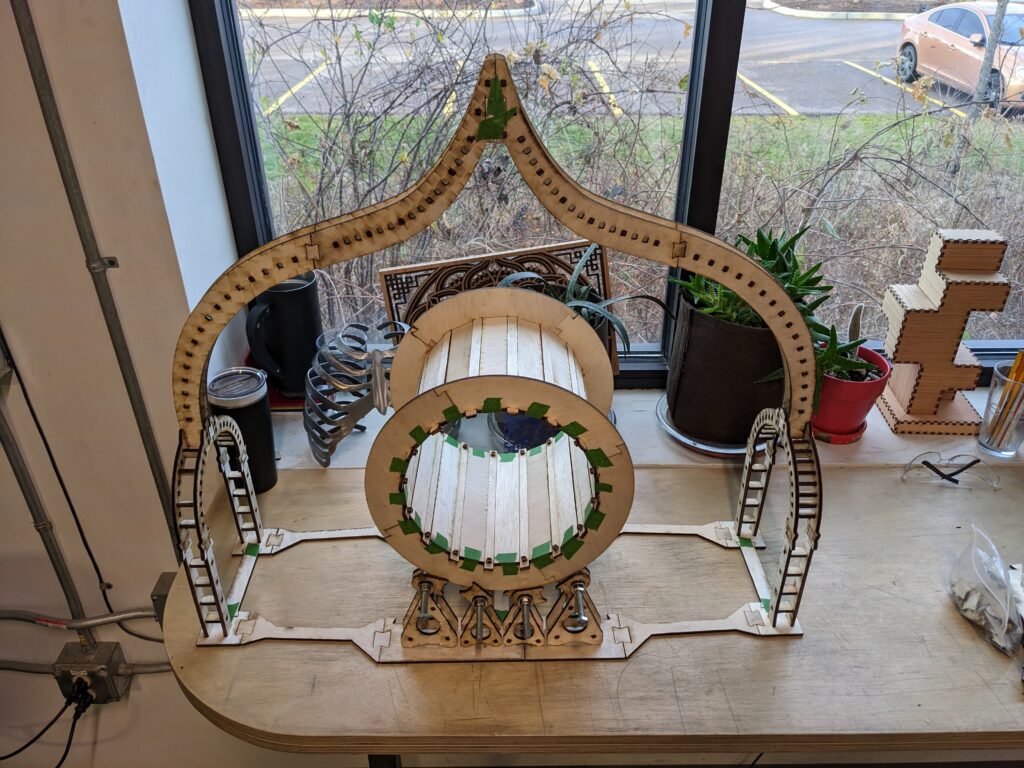
Outer structure assembly